Drill Powered Bike
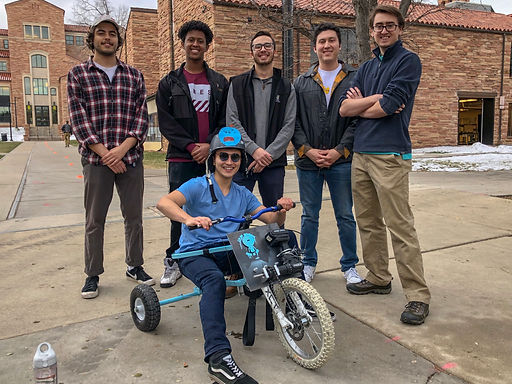_JPG.jpg)
Skills Used
-
Design Basis
-
MATLAB
-
Solidworks
-
Engineering Drawing
-
Material Selection
-
Fabrication​​​​
-
Bandsaw​
-
MIG Weld
-
Mill
-
Lathe
-
Sandblasting
-
-
Integration & Test

Project Description
The challenge of designing and manufacturing a vehicle that is powered by a drill came from my Component Design class. In a team of 6, our team designed a vehicle we thought would put us in an advantage for the maneuverability challenge. The vehicle took form as a tricycle with the capability of the rear wheels assisting in the turn to allow a larger turn radius. With all things said and done, the project was quite a success as we had a real project that worked along with taking home 1st place in the maneuverability challenge!
​
Vehicle Requirements:
-
Vehicle propulsion system shall only be a Makita hand drill
-
Vehicle height shall be less than 30 inches to go under tunnel obstacle
-
Team budget shall not exceed a total cost of $200
​
Personal Contributions:
-
Test Engineer for the team
-
Developed MATLAB code to determine the overall size of the vehicle while maintaining ​obstacle challenge requirements
-
Developed MATLAB code to determine expected castor loads
-
-
Design work
-
Designed the model and produced engineering drawings for the drive train assembly​
-
Modified McMASATER-CARR sprocket design and produced engineering drawing to meet project needs
-
Assembled rear frame components
-
-
Fabrication
-
Used Bandsaw to cut bike's main frame
-
Used Lathe to reduce sprocket's thickness
-
Used Mill to produce a threaded through hole for sprocket
-
MIG Welded bike's main frame together
-
-
Integration
-
Integrated and tested functionality of all components​
-



Lessons Learned
-
Consider all modes of failure when adding in every new component or assembly
-
More time spent in the design and analysis phase means less time spent in the machine shop fabricating new solutions
-
Awareness of everyone's time budget
-
Effective communication is vital for a project to be successful